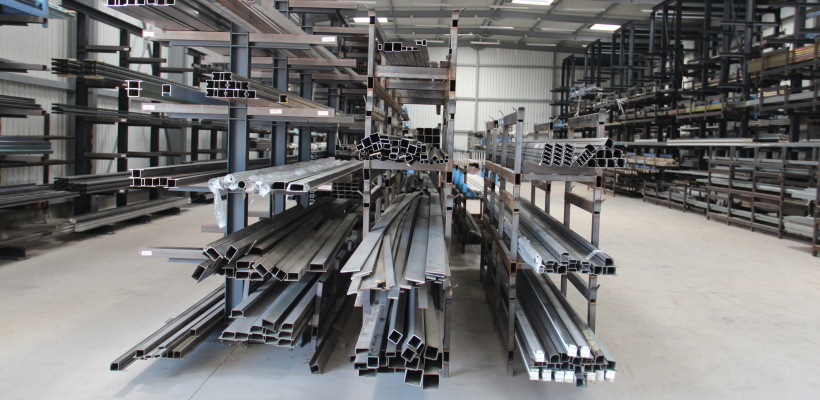
Les quinze dernières années, les méthodes de management visant à chasser la non-qualité et à booster la performance ont gagné du terrain dans les entreprises de métallerie. Le Lean Management en fait partie. Cette méthode issue de l’industrie automobile dans les années soixante, connaît un succès mondial. Elle tend désormais à s’appliquer aussi dans les PME, notamment celles de la construction. Petit rappel : « Lean », en anglais, signifie « maigre ». Le terme à la mode serait « agile » pour désigner une organisation débarrassée du « surpoids ». À ce stade on peut se demander si ça n’est pas une provocation à l’encontre des métalliers qui sont nombreux à se considérer « déjà sur l’os ». En fait, la démarche est plus subtile. Il ne s’agit pas de « dégraisser », mais de réduire les gaspillages. Contrairement aux industries qui privilégient la réduction du personnel pour gagner en performance, dans la métallerie, le Lean n’est pas imaginable sans l’implication du personnel. Ce sont les salariés, à tous les niveaux, qui initient et font vivre la méthode, et plutôt du bas vers le haut que l’inverse. Les salariés sont les meilleurs « chasseurs de gaspi ».
À l’occasion d’une visioconférence initiée par Louis Richard (CMR) en janvier 2021, la consultante Lorette Buys du cabinet POP a mis l’accent sur huit gaspillages à traquer.
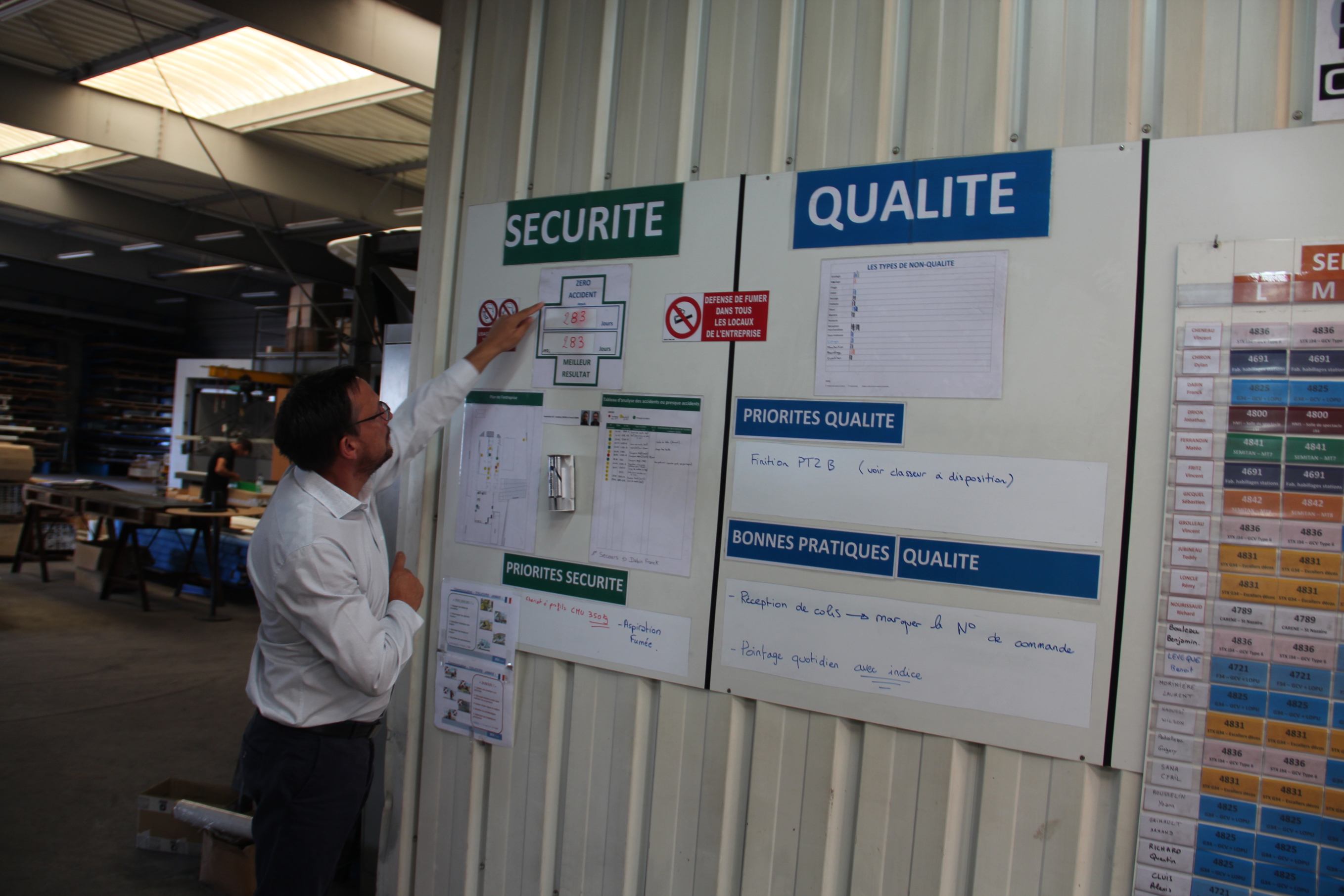
© Pyc
Comme dans toute démarche de qualité, l'implication des équipes est essentielle.
Les huit gaspillages à combattre
1 La surproduction. Pas question ici de « surproduction » de garde-corps ou de platines… C’est dans les bureaux qu’il faut chercher. En 2009, Michel Burtey, ex-dirigeant de Construction Saint-Eloi nous avait dit : « pas la peine de surveiller outre mesure les cols-bleus, ce sont les cols blancs qu’il faut avoir à l’œil ». Personne à l’atelier ne produira plus que nécessaire. En revanche, le bureau d’études peut être tenté de surdimensionner par sécurité. Mettre une tôle de 8 alors qu’une tôle de 6 mm suffirait, par exemple. Les cols blancs peuvent être tentés par une surabondance de réunions, de fichiers, de comptes rendus…
2 La non-qualité. Tout ce qui n’est pas réussi du premier coup. À l’atelier il arrive que l’on se trompe dans les mesures. Cependant les machines sont plus précises et quand le BE envoie le fichier de débit à la machine, si erreur il y a, on sait d’où elle vient… Là aussi, le gaspillage réside dans le fait de ne pas envoyer le bon format, le bon fichier ou tout simplement quand on oublie d’envoyer le fichier… La digitalisation génère de la perte de temps quand les bonnes habitudes ne sont pas acquises. « Ça n’est pas grave en soi, ce qui est grave est de ne pas corriger les récurrences », souligne Lorette Buys.
3 L’attente. Une équipe sur un chantier attend que le ciment sèche… « On paye des gens à attendre ». Il arrive que l’on attende un consommable à 3 euros et que cela bloque la totalité de la chaîne. On attend une personne, une commande, un accord… L’action de construire semble être associée une série plus ou moins longue d’attentes. Le Lean peut contribuer à « fluidifier les interfaces et les process ».
4 Les déplacements. Il y a les déplacements dans l’atelier, les allées-et-venues entre le poste de travail, le magasin, le stock, les bureaux… ils peuvent représenter un poids considérable à la fin de l’année. Pourtant, les déplacements à l’extérieur, l’erreur d’orientation, le chemin plus long, sont moins visibles par la direction et plombent tout autant les résultats en fin d’année.
5 Les mouvements. Il peut arriver en métallerie que l’on déplace régulièrement de la marchandise, des ouvrages, entreposés dans l’atelier, juste parce qu’ils gênent le passage du chariot. On s’y met à trois et on déplace « l’encombrant » qui peut être lourd, voire dangereux…
6 Le stock. Question épineuse. Actuellement stocker des produits dont le prix grimpe en flèche serait un réflexe de bon gestionnaire. Cela n’enlève pas l’intérêt d’une réflexion sur « quoi stocker et pourquoi ? », « ne faut-il pas sous-traiter le stock » ? Cela concerne aussi les cols blancs : « quels fichiers stocker sur le serveur et comment les retrouver ? » Le temps nécessaire pour retrouver un ou plusieurs fichiers peut être considérable et pénalisant.
7 Le surprocess. Il arrive que l’on fasse du « surcontrôle » par habitude. « L’humain est pris dans le confort de l’habitude », indique Lorette Buys.
8 Le gaspillage de compétences. Identifier les talents dans l’entreprise est une chose, les mettre en situation de les exploiter au mieux en est une autre. « Ne pas laisser quelqu’un dans une fonction dormante alors que c’est un avion de chasse », lance la consultante. Sentir par exemple l’âme commerciale chez un technicien.
À ceux qui estiment que le Lean ne serait pas applicable à la métallerie en raison de l’absence de répétabilité, Louis Richard répond « le Lean est une des manières de se poser les bonnes questions, rien d’autre ». Le BIM et la digitalisation en général conduisent de toute manière à revoir notamment l’organisation de l’information. L’essentiel étant de rester pragmatique, proche des salariés, d’éviter d’imposer avec autorité et de ne pas créer des terminologies nouvelles… Avancer à petits pas est la clé, à condition de ne pas s’arrêter de marcher.
Le Lean chez VD Industry
Le spécialiste de la menuiserie de sécurité VD Industry a un process se rapprochant de celui des métalliers. Il a mis en œuvre le Lean en progressant par étapes et en quelques années. « Nous nous sommes focalisés sur l’élimination du gaspillage. Un des pires ennemis du Lean Management : surprocess, stock inutile, transports inutiles (intégration du thermolaquage), mouvements inutiles, gestion de la qualité pointilleuse et recherche d’actions correctives. Via notre logiciel métier, nous avons optimisé les chutes de profilés afin de les réutiliser pour d’autres affaires. La digitalisation nous a aidé à les réduire, voire éliminer les gaspillages : notre ERP mais aussi la mise en place d’une GPAO (Gestion de production assistée par ordinateur). L’autre grand principe du Lean concerne le flux. Notre ERP nous permet une gestion pointue du stock. Il est étudié pour nous permettre de travailler à flux tendu et de servir les clients dans les meilleurs délais. Sa bonne gestion nous permet d’être performant tout en restant compétitifs ». (Source : VD Industry)