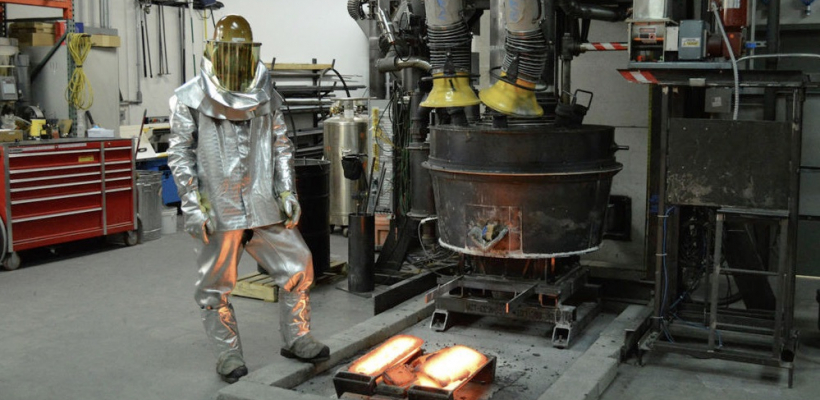
Il suffit d’avoir été une fois sur un site sidérurgique pour prendre la mesure de l’impact écologique du processus traditionnel de production de l’acier. Les émissions de C02 sont considérables. Le secteur sidérurgique serait à lui seul responsable de 5 à 7 % des émissions de GES (gaz à effet de serre). Aussi, il n’est pas absurde de faire un lien entre les débuts de la révolution industrielle au XIXe siècle, marqués par l’avènement de la sidérurgie, et le début du dérèglement climatique. Les excellentes propriétés du métal, à savoir sa durabilité et sa capacité à être facilement trié et recyclé, ne suffisent pas pour lui éviter d’être pointé du doigt dans le contexte climatique actuel. Il y a bien une urgence à traiter la question du mode de production. Celui-ci n’a pour ainsi dire pas changé depuis la première révolution industrielle et certains imaginent aujourd’hui une nouvelle révolution grâce à l’acier dit « zéro carbone ». N’en déplaise aux férus des matériaux biosourcés, il n’est pas possible et pour un moment encore, de pouvoir se passer du métal que ce soit dans la construction, les transports ou les travaux d’infrastructure. Ça n’est pas le matériau qui est en cause, mais le processus qui vise à transformer le minerai de fer en acier.
Réussir à extraire l’oxygène
Pour faire court, ce qui est en cause c’est le principe qui consiste à mélanger dans le haut-fourneau du minerai de fer et du charbon (plus exactement du coke) pour arriver à extraire l’oxygène du minerai à coups de monoxyde de carbone et à très haute température. La fonte obtenue par ce procédé passe ensuite une succession d’étapes visant à en faire un alliage utilisable par l’industrie, dont les multiples nuances d’acier.
La clé est donc bien l’extraction de l’oxygène. Or, c’est là qu’interviennent deux professeurs du MIT (Massachusetts Institute of technology), Donald R. Sadoway et Antoine Allanore. Ce duo de haut niveau travaillait en 2010 pour le compte de la Nasa, l’agence spatiale américaine. Leur mission ? Extraire l’oxygène piégé dans les roches lunaires et, par extension, sur celles d’autres planètes. L’enjeu technologique est immense et on comprend bien pourquoi : il s’agissait de trouver une technique permettant aux équipages stationnés sur ces planètes d’être à terme autonomes en oxygène. De fait, le procédé des deux chercheurs repose sur une électrolyse qui permettrait sur terre de créer du métal fondu dont on aurait extrait l’oxygène sans faire brûler le moindre morceau de charbon. Leur idée, en plus des travaux pour la Nasa, a été de créer en 2012 une entreprise, Boston Metal, pour développer un réacteur de production d’acier zéro carbone.
Une anode en chrome
Comme le précise le journaliste Pierre Fortin dans un article publié dans Les Échos datant du 5 mai 2021, « L’électrolyse du minerai de fer consiste à faire passer entre les deux pôles d’un réacteur – l’anode et la cathode – un courant électrique capable de chauffer le métal tout en séparant les ions du fer des ions de l’oxygène grâce aux électrons qui remplacent le monoxyde de carbone ». Cette technique engendrerait même un acier de meilleure qualité. Aussi, afin d’éviter d’utiliser une anode en carbone, elle est remplacée par un équivalent en chrome qui ne se corrode pas sous l’effet des dégagements de molécules oxygène. Ce procédé appelé MOE (molten oxide electrolyisis) ne dégage que de l’oxygène sans consommer d’eau ou des réactifs. Reste évidemment à s’assurer d’une alimentation en électricité décarbonée, ce qui est largement le cas de la France notamment grâce à son parc de centrales nucléaires.
Bien que les chercheurs du MIT aient réussi à lever près de 100 millions de dollars auprès d’investisseurs aussi multiples que Bill Gates ou le groupe automobile BMW, la production actuelle n’a pas encore dépassé 1 tonne. Vers 2024, Boston Metal espère atteindre une vitesse de croisière industrielle en commercialisant des licences et les anodes inertes à base de chrome. Plusieurs inconnues demeurent cependant. À commencer par l’attitude des sidérurgistes. Franchiront-ils ce pas qui aura pour conséquence de bouleverser entièrement la chaîne de fabrication ? Les promoteurs du MOE expliquent que cette solution permettra de baisser de 35 % les coûts d’approvisionnements en matière ne serait-ce que par la suppression des achats de charbon. Le basculement ne se fera pas d’un coup, c’est une évidence. Cependant, en installant ces centres sidérurgiques à la fois près de zones d’extraction et de zones de production d’électricité, par exemple hydraulique, les coûts et l’impact environnemental lié au transport seraient sensiblement réduits. L’aluminium (avec l’exemple du groupe Hydro) avait déjà emprunté cette voie et il n’est pas étonnant de retrouver les pays scandinaves (voir encadré) riches en barrages aux avant-postes de la recherche dans ce domaine.
Si le prix de l’acier devait malgré tout grimper par ces nouvelles technologies de production, il est vraisemblable que la part du réemploi augmenterait parallèlement. Une boucle vertueuse s’enclencherait alors pour le bénéfice de tous et en premier lieu pour l’environnement.