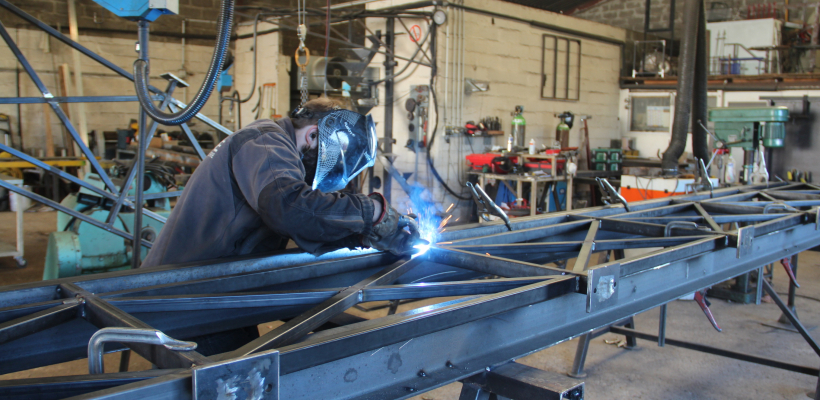
On peut sans doute se passer d’un certain nombre de machines en métallerie, nous ne les citerons pas. Mais un atelier sans poste à souder est quasiment impossible à trouver… C’est l’outil et l’investissement de base par excellence. En MIG/MAG, en TIG ou à électrodes enrobées ces équipements font partie intégrante du métier. Cependant, au cours des dernières décennies, les matériels ont connu des progrès considérables avec la digitalisation : sur le plan des afficheurs, de la consommation d’énergie, sur les programmes embarqués voire sur la connectivité des postes. Les réglages sont potentiellement définis par la machine selon la nature du métal et selon son épaisseur.
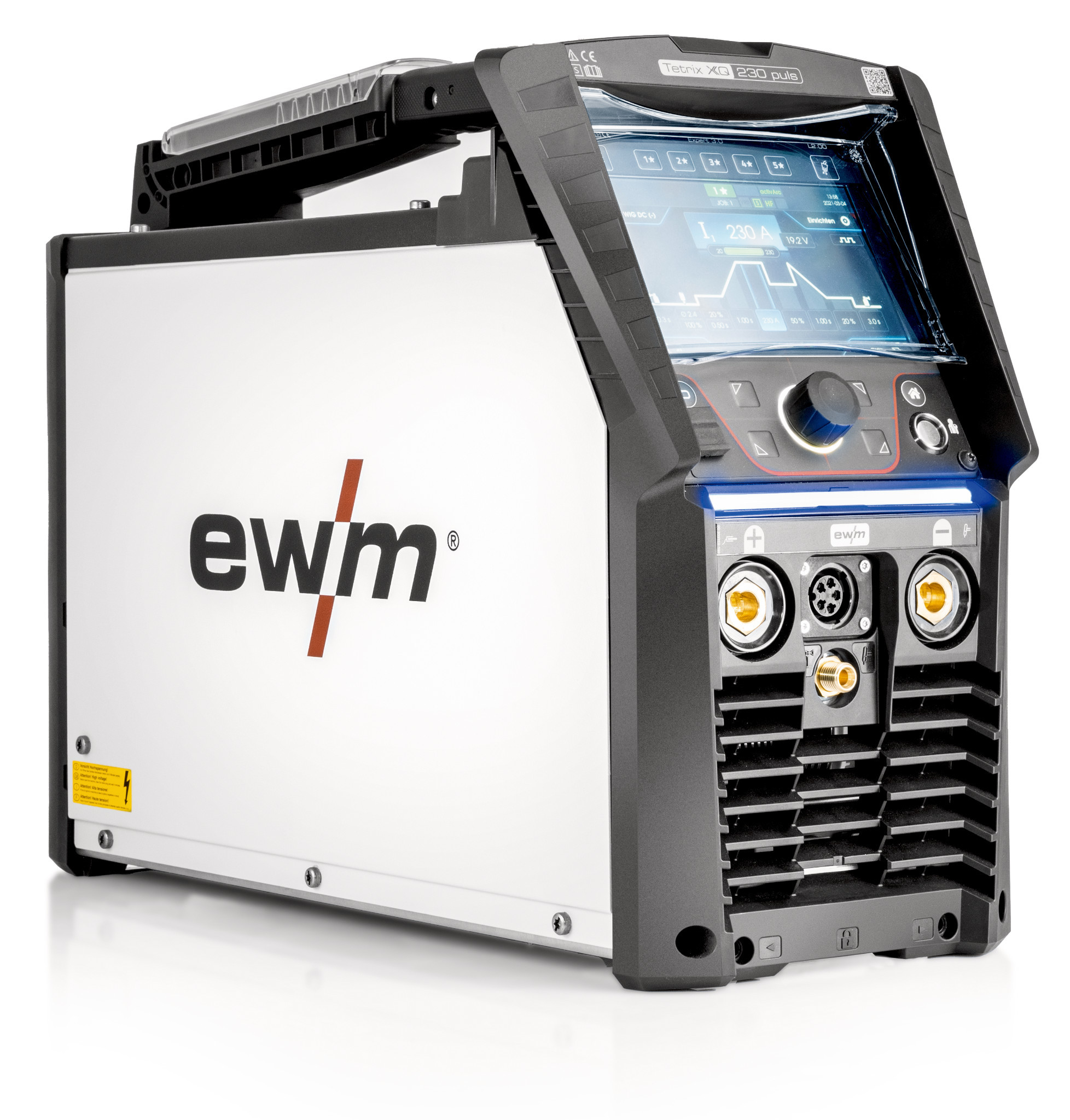
Outils de traçabilité
Il y a désormais la possibilité d’assurer une traçabilité rigoureuse qui peut être, à terme, exigée par le marché. En quoi ces évolutions peuvent-elles améliorer la performance et l’attractivité des entreprises ? Est-il devenu plus facile de souder aujourd’hui ? Quels sont les fabricants les plus en pointe sur la technologie et sur le service ? Qu’en est-il des postes multiprocédés ? Et comment choisir parmi la foison d’appareils disponibles ?
Éléments de réponses avec Christophe Lagarde dirigeant de System Weld et animateur youtubeur à succès du site Soudeurs 2.0. Il est aussi co-organisateur des Championnats de France de soudure (26 au 28 mai 2023 à Vierzon).

Métal Flash Quelles grandes évolutions techniques faut-il retenir des vingt dernières années ?
Christophe Lagarde On peut citer la consommation électrique qui a nettement diminué. À une époque on consommait bien plus que l’on n’avait besoin. Les progrès ont été considérables sur l’énergie.
Ensuite les modes synergie ou synergiques. Ce sont les programmes qui facilitent l’utilisation et le réglage du poste. Avec un minimum d’informations on obtient le programme adéquat. C’est utile quand on a des soudeurs peu expérimentés dans l’entreprise. On donne le matériau, l’épaisseur… et on est moins perdu. Depuis 15 ans c’est une tendance lourde chez les fabricants de produits professionnels. Enfin, les postes connectés. Toutes les grandes marques sont capables de proposer des solutions connectées. Est-ce vraiment utile ? En fait, sur son téléphone ou sur l’ordinateur, on peut avoir les temps de soudage, la consommation d’énergie… Certains clients pourraient demander ça dans le cadre de projets en basse consommation. Les relevés de paramètres seraient autrement difficiles à transmettre au client. Les donneurs d’ordres peuvent demander des relevés, avec la connexion c’est réalisé automatiquement, un gain de temps en traçabilité. C’est aussi un moyen de retrouver pour le soudeur, les paramètres qu’il a appliqués sur un ouvrage pour les reproduire à un autre moment. Utile pour l’aluminium notamment.
M. F. Tous les fabricants ou presque proposent des postes multiprocédés, est-ce véritablement un progrès ?
C. L. Les postes multiprocédés abordables et capables de faire du MIG, du TIG et de l’électrode enrobée n’ont pas été un grand succès commercial. Le TIG est un peu la « bête noire » du soudage, il a besoin de hautes fréquences ce que les multiprocédés à 2 000 ou 3 000 euros ne permettent pas d’avoir. Par contre, chez les fournisseurs de matériels pros de niveau solide il y a des multiprocédés nettement plus chers qui permettent d’avoir un poste pour plusieurs technologies de soudage. L’inconvénient de ces appareils reste qu’en cas de panne, on est tout nu… C’est ce qui freine un peu cet investissement.
M. F. Il semble que les fabricants européens et américains tiennent encore bien leur marché. Qu’en est-il ?
C. L. Les fabricants européens et américains restent solides en industrie et en métallerie. Pourtant il y a du bon matériel en Asie. Le parc européen tient bien, grâce à la qualité et au service. On a des fabricants de Finlande, d’Autriche, d’Allemagne et même de France qui tiennent bien la route. On parle d’obsolescence programmée dans les matériels électroniques or ça ne se vérifie pas sur les postes à souder. C’est un investissement lourd, ce n’est pas un consommable, on n’a pas intérêt à changer le poste tous les cinq ans. Il y a des mises à jour, du SAV et des retrofits proposés par les fabricants premium. Les Européens sont fiables et durables. Je vois peu de matériel en panne.
M. F. Peut-on dire qu’il est devenu plus facile de souder correctement aujourd’hui ?
C. L. Ça dépend sur quelle technologie on s’appuie. En MIG / MAG oui clairement c’est devenu plus facile de réussir les cordons et ce sur la durée. Mais ça n’est pas le cas en TIG où il faut avoir de l’expérience. Idem pour l’électrode. Les certifications sont toujours demandées.
M.F. Quels sont selon vous les meilleurs postes ?
C. L. En TIG je mets sur la même ligne d’arrivée chez EWM le Tetrix 230 et le iWave de Fronius. Ce sont des piliers dans leur catégorie, avec un arc extrêmement stable. En semi-auto j’ai une préférence pour le TPS/i de Fronius, je l’ai en 320 A, c’est pour moi le meilleur poste dans sa catégorie.

Quelle stratégie adopter pour les postes à souder ?
J’ai traversé plus de 17 ateliers de fabrication en intérim. De la machine agricole aux engins de carrières avec convoyeurs, en passant par les portails et les garde-corps, pour finir en agroalimentaire Inox, j’ai touché à divers secteurs. Ce qui m’a toujours frappé, c’est la disparité des marques de postes à souder et la difficulté à s’y adapter à chaque nouvelle mission. Quand on n’est pas soudeur de métier, il peut s’avérer contraignant de prendre ses marques au démarrage d’une mission ou de passer du TIG au Mig Pulsé. Le progrès technologique en matière de postes à souder est encore peu envisagé dans les PME et TPE, que ce soit des métalleries / serrureries ou des chaudronneries, autrement que comme une dépense. Pourtant, il est tellement facile de compenser un investissement par de la productivité et du management ! Oui le poste à souder peut devenir un outil d’intégration et de management.
Uniformisation des façades et facilité de prise en main
Il est possible d’utiliser les façades machines comme un véritable « livret d’accueil » du nouveau salarié ou de l’intérimaire : souvent il suffit d’un visuel avec l’explication permettant de chercher les programmes par références, par type de fabrication, par code affaire ou synergies de courant. Partir du principe que les métalliers ou les chaudronniers sont des soudeurs qualifiés au sortir de leur formation est une erreur. Ils le deviennent par l’expérience. On dit bien qu’un semi auto se règle « à l’oreille » ? Confier des postes à souder dans lesquels sont chargées les désignations des fabrications récurrentes, en les connectant au réseau (ou en connectant le poste à un PC) est source de confort de travail et de conformité des fabrications. Avec la garantie de consommations de gaz égales et les mêmes avances de fil (à +/- 10 % selon la « patte » de la personne). Les soudeurs métalliers remonteront en retour les améliorations possibles sur les réglages de poste. La communication devient plus horizontale entre l’atelier et le bureau d’études, avec moins de frustration de la part des équipes de l’atelier. Améliorer la qualité des cordons de soudure, c’est un gain à tous les niveaux. Notamment une baisse de consommation de disques abrasifs pour effacer « le massacre », des rendus après peinture de bien meilleure qualité, des temps de soudage réduits… Au moment de souder, on appelle le programme correspondant à sa fabrication, ce qui implique beaucoup moins d’erreurs possibles avec en prime la traçabilité des temps de fabrication. Ainsi, la marge nette sera plus précise en comparant le temps passé en soudage, par rapport au temps vendu.
Conformité à la norme EN 1090
Plusieurs marques fabriquent leurs sources de soudage et également leurs métaux d’apports. Les postes peuvent contenir des programmes et des synergies qui prérèglent la source en conformité avec une QMOS (Qualification de Mode Opératoire de Soudage). Cette QMOS, si le métallier est aussi qualifié en EN ISO 9606, permet des fabrications conformes à la norme EN 1090. C’est impératif pour les travaux structurels de type charpentes, mezzanine, extentions...
Suivre la validité et le renouvellement des QS (Qualifications de soudure) des chaudronniers est parfois fastidieux. Désormais, certaines marques incluent un rappel des échéances afin de ne plus le rater. Combien de fois a-t-il fallu repasser une QS en urgence car expirée ?
Windows ou Mac OS ?
Si les salariés du tertiaire se sont approprié l’outil informatique, gagnant ainsi en productivité, c’est notamment grâce à l’uniformité des modes de fonctionnement. Que l’on soit PC ou Mac, on retrouve toujours la même interface sur son PC. Quand on change de fonction et/ou de matériel informatique, on n’est pas perdu avec ses outils. Clairement, je n’ai jamais vu une métallerie ou une chaudronnerie accueillir ses nouveaux arrivants en leur remettant un manuel des postes à souder ou une explication du fonctionnement des postes. Aborder le soudage de la même façon qu’on aborde les smartphones ou les PC permettra d’intégrer au mieux les nouvelles générations.