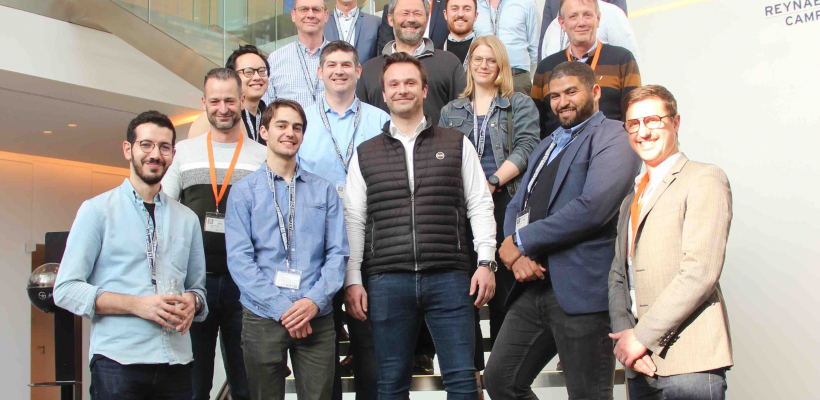
Voyage entre alu et fer
Depuis que le gammiste aluminium belge a racheté en 2017 le gammiste acier suisse Forster, l’intérêt des métalliers pour la marque a logiquement grandi. Avoir l’aluminium et l’acier sous un même toit permet d’avoir un discours plus détendu sur les atouts et les limites de l’un et de l’autre. Or, les métalliers comme les BE et les architectes, sont avant tout demandeurs d’arguments techniques solides et de solutions fiables. C’est sans doute dans cet esprit que l’équipe de Forster France a organisé un voyage de deux jours en Belgique, les 23 et 24 mars derniers. Le premier jour a été dédié à la découverte du siège social de l’entreprise familiale à Duffel en Flandre. La quinzaine d’invités a eu l’occasion de découvrir le campus Reynaers qui comprend un showroom (avec les gammes des deux marques), le centre d’essais et de formation ainsi qu’une salle de visualisation 3D. Cette technologie appelée Avalon, permet, après un travail de conversion des plans en format Revit (destiné au BIM) de pouvoir se projeter avec des lunettes spécifiques dans le futur bâtiment. Cette expérience de réalité virtuelle ne se généralisera pas pour les chantiers en rénovation ou pour les opérations de taille modeste. Elle est cependant comme l’a fait remarquer un des BE présents « un outil commercial puissant pour les grands ensembles tertiaires pour lesquels les maîtres d’ouvrage ont besoin d’arrêter des choix techniques et esthétiques ». Un des métalliers présents a fait remarquer qu’il serait tentant « d’imaginer visualiser et se déplacer dans un atelier de métallerie en 3D pour pouvoir optimiser le positionnement des machines et des postes de travail » avec cette technologie.
Aux limites de l’extrême
Le lendemain c’est à une expérience bien réelle qu’ont eu droit les invités : le site sidérurgique d’ArcelorMittal à Gand. La découverte d’un tel process de fabrication reste un moment marquant. Entre la zone des matières premières qui arrivent essentiellement par bateaux, la cokerie où le charbon est transformé en coke, le haut-fourneau, la coulée continue, le laminoir… il y a de quoi être impressionné. Les dimensions gigantesques (un site de 850 hectares), les effets visuels et surtout la chaleur inouïe (jusqu’à 1 500 °C) qui se dégage sur certains postes ne laissent personne insensible. À Gand, ArcelorMittal produit des brames qui sont ensuite laminés pour devenir des bobines de tôle. Avec des guides experts et passionnés, les visiteurs découvrent comment cette industrie d’apparence grossière est capable de travailler avec une extrême précision tant sur les alliages à produire que sur les épaisseurs et les dimensions. Aussi, l’usine de Gand s’est engagée dans un important programme de décarbonisation qui devrait, avec un investissement de 1,1 milliard d’euros, permettre de réduire de 3,9 millions de tonnes les émissions de CO2 d’ici 2030. L’idée est de sortir du process à base de charbon pour se tourner vers les fours électriques et la réduction directe (DRI « direct reduced iron »). Sachant que l’acier de Forster provient en majeure partie du site de Gand, cette information ne devrait pas laisser insensible les amateurs de menuiseries acier.
Métalleries participantes : Blanchet, Calser, Loison, Oxium, Réseau Fermetures, SMC.
BE participants : Arcora, EOC, VS-A.